拖拉机变速箱是拖拉机的核心部件,拖拉机变速箱经常会出现异响、噪声大、齿轮打齿等故障,根据目前的经验判断,与变速箱内的齿轮及齿轮轴等的质量有很大的关系。齿轮类零件是由专业生产齿轮的厂家提供的,齿轮从毛坯到加工为成品再到装配到齿轮箱中,中间有很多的流通环节,会对齿轮的齿面质量造成影响,因此在将齿轮装配到变速箱前,快速挑出有质量隐患的齿轮类零件变得尤为重要。现状是只能对齿轮的齿形、齿向、齿圈径向跳动、齿距累积总偏差进行检测,而没有检测手段可以检测齿轮径向综合总偏差 F″i 和一齿径向综合偏差 f″i 等。为了提高齿轮类零件的检测手段,快速挑出齿面有毛刺或有划痕的齿轮以及检验齿轮啮合后的接触印迹情况,作者采取齿轮双面啮合综合测量仪配合标准齿轮来进行齿轮径向综合总偏差 F″i 和一齿径向综合偏差 f ″i 的快速检测。文中主要从双啮仪的设计以及标准配对齿轮两个方面阐述了齿轮径向综合偏差检测。
2 双面啮合综合测量仪
径向综合偏差属于综合参数偏差,它主要影响齿轮传递运动的准确性和传动的平稳性。从齿轮旋转一周记录下的曲线 ( 如图 1 所示) 可以看出: 误差曲线中包含明显的一次谐波曲线,其中 F″i 为齿轮径向综合总偏差,f″i 为一齿径向综合偏差。此外,从图中还可揭示出齿廓偏差,一个较大的齿距偏差或受损伤的轮齿。目前,由于齿轮径向综合偏差检测仪器 ( 如双啮仪) 结构简单,操作维护方便,测量效率高,能适应相对恶劣的生产现场环境以及实现被加工齿轮 100% 检测等优点,生产中广泛采用。
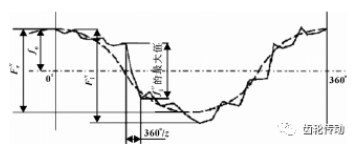
图 1 径向综合偏差
文中采用的双面啮合综合测量仪的结构如图 2 所示,检测齿轮径向综合偏差的方法主要是: 基于齿轮双面啮合原理,将被测齿轮安装在固定轴上,测量齿轮安装在带有滑道的浮动轴上,该滑道带一弹簧装置,从而使两个齿轮在径向紧密地啮合,转动被测齿轮一周,其中心距的最大变化量即为径向综合总偏差 F″i,转过一个齿距角时中心距的最大变动量即为一齿径向综合总偏差 f″i。其测量原理如图 2 所示。
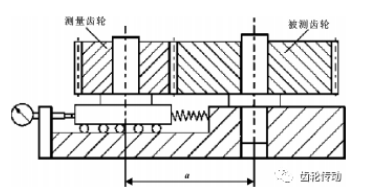
图 2 双面啮合综合测量仪的结构示意图
3 标准齿轮设计
检测用标准齿轮 ( 后简称标准齿轮) 主要用于齿轮的双面啮合检查。在齿轮的加工过程中,热处理前、后齿形部分及热处理等加工和运输过程中会出现残留毛刺和磕碰现象。检测用标准齿轮就是根据齿轮的无侧隙啮合原理,通过待检齿轮与标准齿轮紧密啮合转动一周,从啮合过程中的震动或双啮仪上百分表读数的变动量,来判断整个齿面上是否有磕碰、未去除的毛刺。
标准齿轮与待检齿轮的啮合属于平行轴的圆柱齿轮的啮合范畴,按照圆柱齿轮进行设计即可,因不传递扭矩,强度、硬度要求不高,故此类齿轮只做齿形及结构设计,不做强度校核。标准齿轮具体设计方法如下:
(1) 标准齿轮齿数的要求
根据机床结构和标准齿轮的结构特点确定。机床的结构决定啮合中心距,根据中心距计算标准齿轮的齿数,圆整,要求与待检齿轮齿数互质,并尽可能地取多齿数,这样会提高标准齿轮的寿命。
(2) 标准齿轮齿厚的要求
尽量满足两齿轮啮合时,节圆与分度圆一致。标准齿轮的使用目的不一样,设计方式也不同。如综合检查用标准齿轮,是真实模拟配对齿轮啮合状态中的误差,这样设计标准齿轮时要尽量保证标准齿轮的齿厚和待检齿轮的配对齿轮相同,使其啮合状态与使用状态一致; 而啮合检查用标准齿轮则只是检查齿轮的毛刺、磕碰等,故只需有效齿面内全接触皆可,齿厚不做严格要求。变速器齿轮多为非标准齿轮,采用细长齿,且根据强度的要求,有一定的变位系数 x1,标准齿轮的变位系数取x0 = - x1,即标准齿轮和待检齿轮的齿厚之和等于其分度圆齿厚,仅以此作为一个设计基准,可调整。
(3) 标准齿轮渐开线起始圆直径的要求
渐开线有效齿形要覆盖待检齿轮的齿顶圆,因目前生产的变速箱齿轮在齿顶有径向 0. 2 ~ 0. 4 mm 的倒角,实际渐开线不能到达齿顶外圆位置,0. 2 ~ 0. 4 mm 的径向尺寸可以当作标准齿轮设计时渐开线起始圆位置的安全系数,不用再另增长渐开线的有效长度,只需按照待检齿轮外圆尺寸设计即可。
(4) 标准齿轮渐开线终止圆直径的要求 (外径)
要保证待检齿轮齿形全长被检测,标准齿轮的齿形要覆盖待检齿轮的渐开线起始圆直径并有一定的安全系数,即标准齿轮的齿顶圆直径要达到待检齿轮的渐开线起始圆并要求一个超越量,参照剃齿刀设计时的超越量标准,同时要保证与待检齿轮齿根圆间的径向间隙不小于 0. 25 mn,并验证标准齿轮齿顶是否变尖。
(5) 标准齿轮齿根圆直径的要求
保证与待检齿轮齿顶圆间的径向间隙,在齿轮副设计过程中径向间隙一般取 0. 25 mn,标准齿轮齿根圆直径按照径向间隙系数为 0. 25 设计。
(6) 标准齿轮齿宽的要求
作为检查用标准齿轮,标准齿轮在齿宽方向要将待检齿轮全部覆盖,通常比待检齿轮宽 2 ~ 4 mm。
(7) 精度等级的要求
标准齿轮用于生产齿轮的检验,其精度等级要在待检齿轮的精度等级上提高 2 ~ 3 个等级,齿轮精度一般为 7 级,标准齿轮多定为 5 级,标准应与待检齿轮的标准一致,文中按 GB/T 877标准。作者按照上面的规则选取了生产中经常接触的几十种齿轮进行了齿轮的标准配对。
4 测量结果
齿轮的双面啮合仪加上配对的标准齿轮制作完毕,如图 3、 图 4 所示。
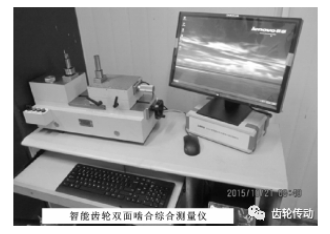
图 3 齿轮双面啮合仪
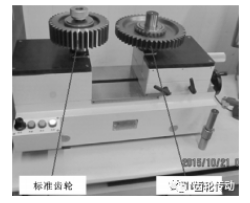
图 4 齿轮双面啮合仪的标准配对齿轮和被测齿轮
通过使用双面啮合综合测量仪,圆柱齿轮径向综合总偏差 F″i 和一齿径向综合偏差 f″i 以及齿圈径向跳动 F″r 都可以被检测,如图 5 所示。
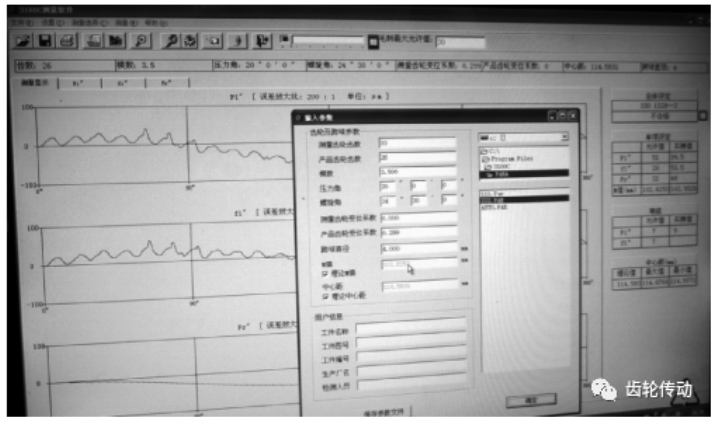
图 5 齿轮双面啮合仪的测量结果
此次测量结果见表 1,径向综合总偏差 F″i、一齿径向综合偏差 f″i、齿圈径向跳动 F″r 均超差,测量结果不合格。拆下被测齿轮发现齿面有磕碰伤、毛刺。用双啮仪初步检测齿轮的 3 个参数可以迅速地检出齿面上的磕碰伤、毛刺,在被测齿轮齿面上涂一层红丹粉,通过与标准齿轮进行无间隙啮合后,观察齿面啮合情况,检查齿轮的实际啮合情况,可以判断出齿轮运转中是否会出现异响、打齿、偏磨等故障,为齿轮的快速检测提供了有力的手段。
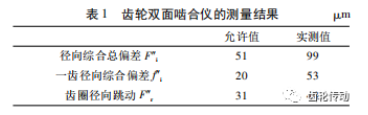
5 结论
经过验证,使用双面啮合综合测量仪,可以检测圆柱齿轮径向综合总偏差 F″i、一齿径向综合偏差 f″i 以及齿圈径向跳动 F″r,特别是齿面上的磕碰伤、毛刺这些引起齿轮异响主要原因的项目,用双啮仪能够自动准确地找到; 另外在被测齿轮齿面上涂一层红丹粉,通过与标准齿轮进行无间隙啮合后,观察齿面啮合情况,可以判断出齿轮运转中是否会出现异响、打齿、偏磨等故障,为解决变速箱异响提供有效的手段。