满足不断变化的齿轮检测需求的解决方案
“生产机器如何影响齿轮噪音?附近的其他设备是否会引起额外的振动?这些都是需要回答的问题,以更好地了解齿轮噪音,“格里森计量系统国际销售经理KlausDeininger说。
“齿轮功率密度的不断增加和噪声行为的重要性日益增加,导致公差越来越严格,从而给齿轮检测技术带来了更大的负担,”Deininger说。
即使所有测量值都处于公差范围内,组件仍然会因不良噪声行为而失效。格里森提供两种软件应用程序来评估齿轮噪声,包括低频噪声、中频噪声和高频噪声(加冕、齿网不规则性和波纹度):
GAMA的KTEPS(运动学传动误差预测软件)通过部署齿形测量来分析整个齿轮旋转的接触平面。基于表面偏差,可以通过FFT分析计算和评估传输误差。在第二步中,操作员可以通过仅提取代表可疑谐波的形貌数据来评估可疑谐波。这些数据以假彩色图片呈现,使得更容易理解波纹的来源。这种独特的齿轮评估方式是鬼影噪声研究的理想工具,同时与线束单侧翼测试相关联。
形貌测量是一个相对缓慢的过程,因此客户希望比过去更快、更有效地获得波纹度测量。格里森创建了高级波纹度分析,以检测和减轻由难以发现的牙齿形状不规则引起的关键噪声行为。高级波纹度分析软件可以与KISSsoft的装载TCA齿轮设计软件无缝连接,以提供基于标准轮廓,引线和螺距检测的多传感器检测齿轮噪声分析,可以是触觉,光学或两者的组合。
“这将是在当今生产环境中获得客户所需测量的更快方法。没有额外的分析时间,一旦测量完成,你就会得到结果,“Deininger说。
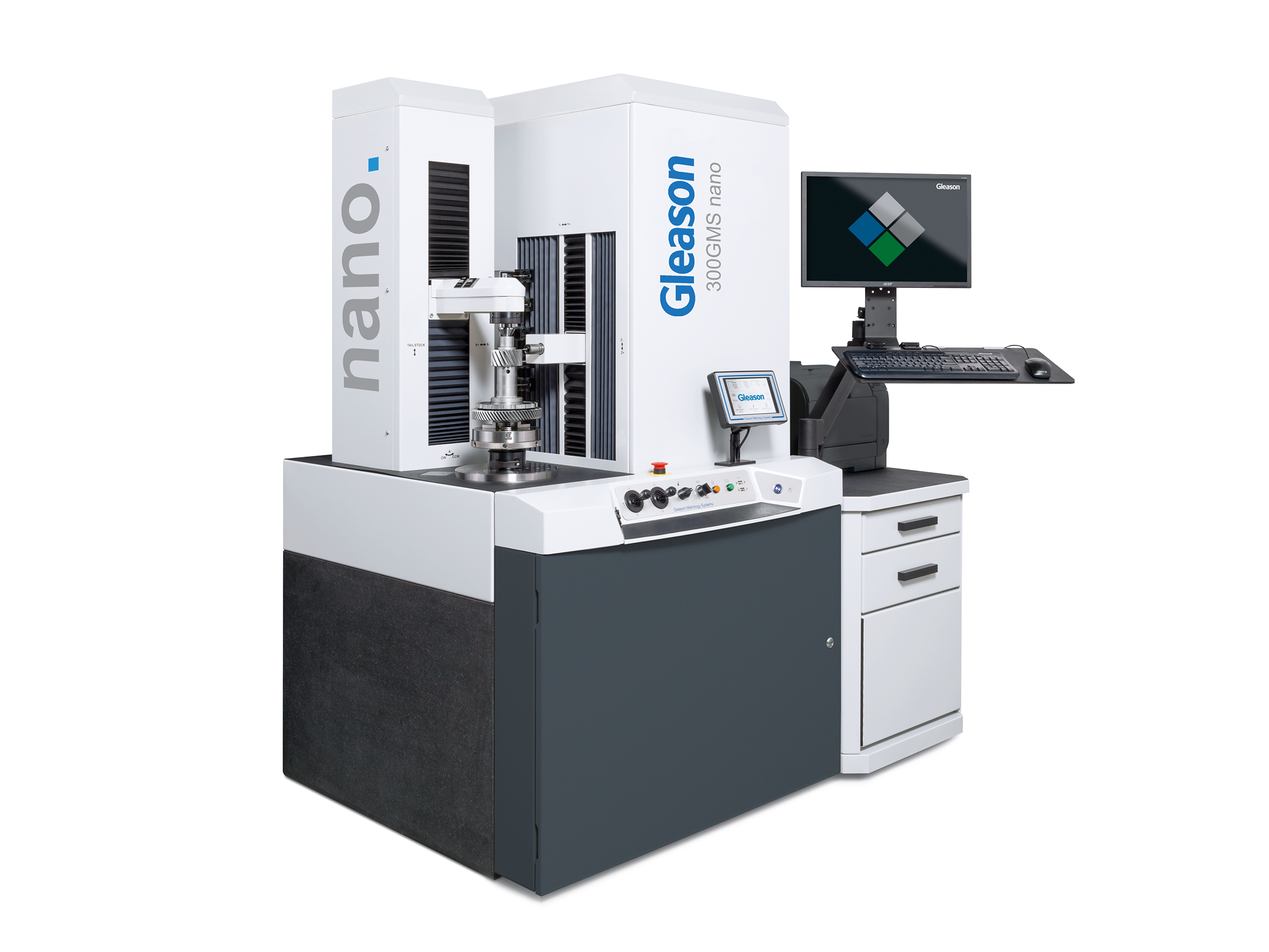
具有集成齿轮噪声分析的300GMS纳米齿轮计量系统。
300GMSnano是新检测系统的一个例子,该系统适用于支持汽车电驱动生产,噪音要求最低。
“这台机器涵盖了现代齿轮检测的全部功能,以及细间距齿轮检测和CMM测量。使用300GMSnano,用户现在能够使用无撬探头测量亚微米级的表面光洁度,分析轮廓,铅和间距的波纹度,并使用复杂的软件工具执行噪声分析,“他补充说。
该机器还集成了通常由CMM提供的3D测量和分析功能。300GMSnano为客户提供了电驱动齿轮测量的宝贵工具。
几十年来,齿轮噪声NVH辊测试一直是锥齿轮生产的一部分,但圆柱辊测试市场需要更复杂的技术。
“为了研究电动汽车,我们必须从低频到高频水平检查NVH,并提供各种测试特性和功能,”Deininger指出。
格里森的GRSL(齿轮轧制系统与集成激光技术)系统将传统的轧辊测试与先进的非接触式激光技术相结合。这大大缩短了指数、引线和轮廓检测以及齿轮噪声评估的周期时间,并提供了100%生产输出的分析检测,即使对于最严苛的齿轮应用也是如此。
将GRSL与高级波纹度分析软件相结合,提供了独特的可能性,可以评估每个齿轮在齿面上的潜在波纹度,这是齿轮啮合中高频噪声的最终贡献者。这意味着,没有具有可疑或不良噪声行为的齿轮进入最终装配,从而大大减少了具有不良噪声行为的齿轮箱的昂贵拆卸。当今的齿轮检测还必须考虑机器行为本身。机器如何为测量做出贡献?为什么机器之间有变化?格里森如何提供最准确的检测结果?
最近,GRSL系统被集成到格里森的硬精加工单元(HFC)中。该自动化系统包括一个机器人,该机器人集成了各种工艺模块,包括齿轮磨削,清洗,激光打标,测量和零件处理。在齿轮检测期间,激光扫描仪为每个齿提供测量特性。偏差通过闭环校正反馈到机器中。
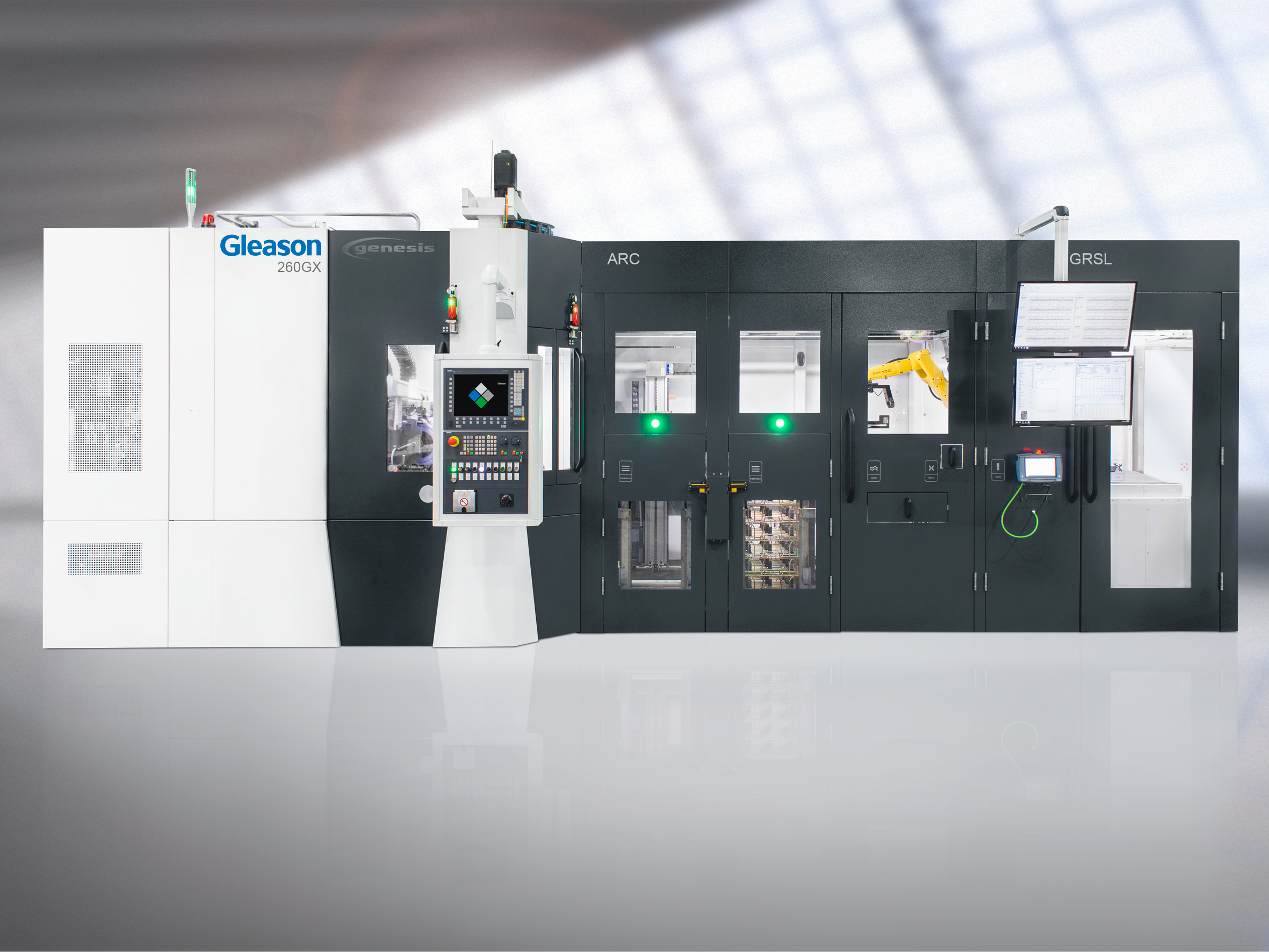
格里森的HFC硬精加工单元将齿轮磨削、辅助工艺和齿轮检测与完全机器人化的零件处理相结合。
齿轮检测的未来是完整的,在闭环自动化系统中集成齿轮噪声分析的过程内测量,为客户提供所有必要的手段,以始终保持公差,最大限度地减少废品和返工。
克林贝格剖析复杂的检测要求
克林贝格精密计量总监ChristofGorgels博士讨论了近年来汽车行业齿轮公差的降低问题。“对噪声性能测试的需求增加了,并且是传统几何质量评估的补充。通过齿轮偏差分析(GDA),Klingelnberg多年来一直提供一种工具,仅基于简单的齿轮测量来分析齿轮的预期噪声行为,“他说。
凭借克林贝格的混合方法,该公司提供了一种在不影响准确性的情况下实现更快测量的解决方案。此外,R300 a 辊子测试解决方案可以在生产周期内对齿轮进行快速的100%噪声评估。
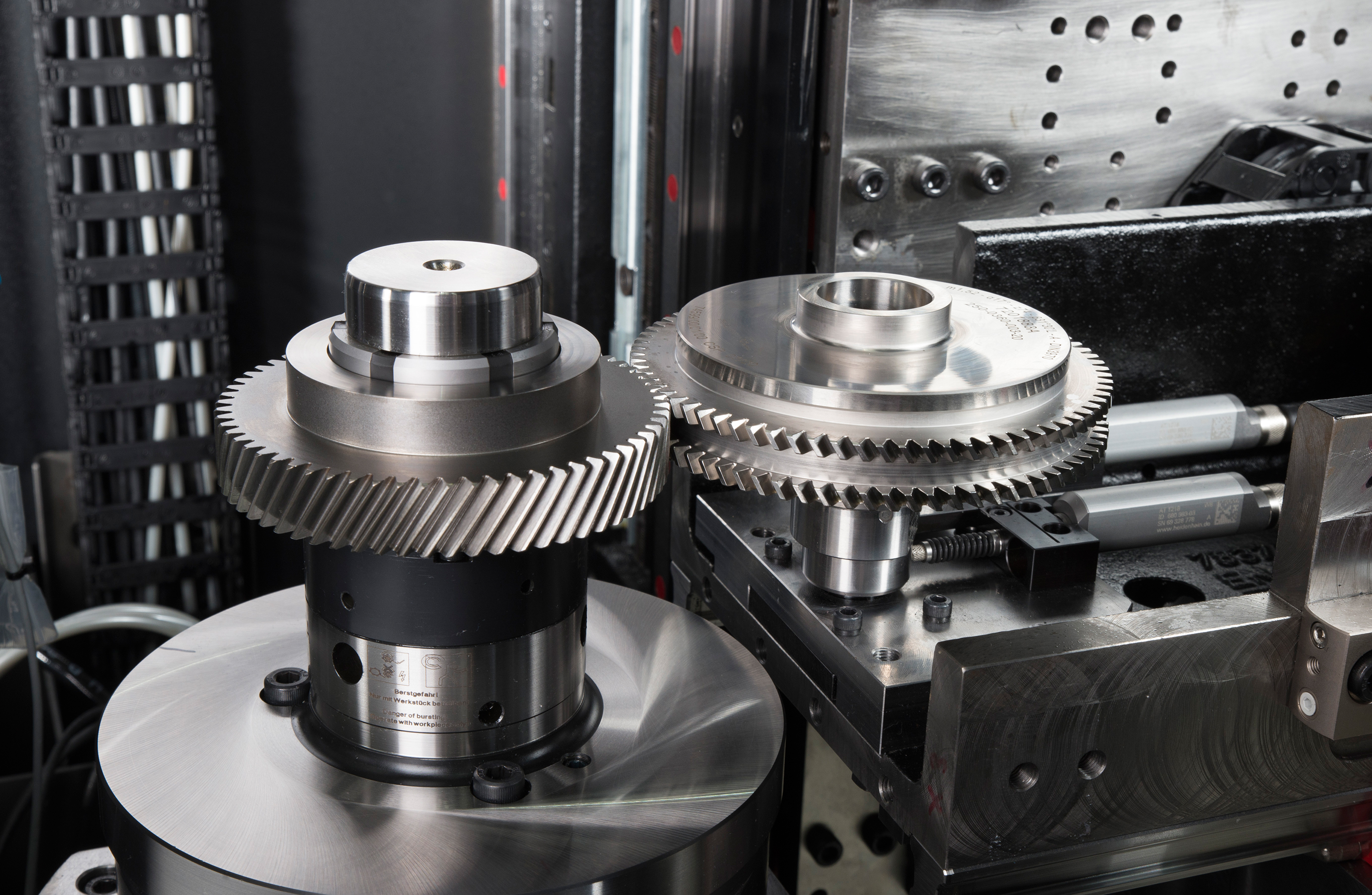
R300 提供五种侧倾测试方法,包括单侧翼、结构承载、扭转加速度、双侧翼和螺旋滚动测试。
“速度和灵活性都有助于最大限度地降低质量成本,”Gorgels说。“通过结合GDA、混合计量和辊压测试,克林贝格为齿轮在几何质量和噪音方面的不同要求提供了解决方案。
与传统车辆相比,电动汽车有两个主要区别:“最明显的是发动机缺乏遮蔽噪音,使齿轮噪音更加突出。从承载能力来看,电动机具有不同的扭矩特性,从而增加了驱动侧翼的负载。此外,回收导致海岸侧的高负荷,这对汽车行业来说是新的。将更高的负载和噪音要求与高负载的海岸侧翼相结合,齿轮侧翼设计的优化变得更加复杂,“Gorgels说。
克林伯格的GDA软件使齿轮噪音可见。它包括四个模块视图,波浪分析,波浪生产和生产。
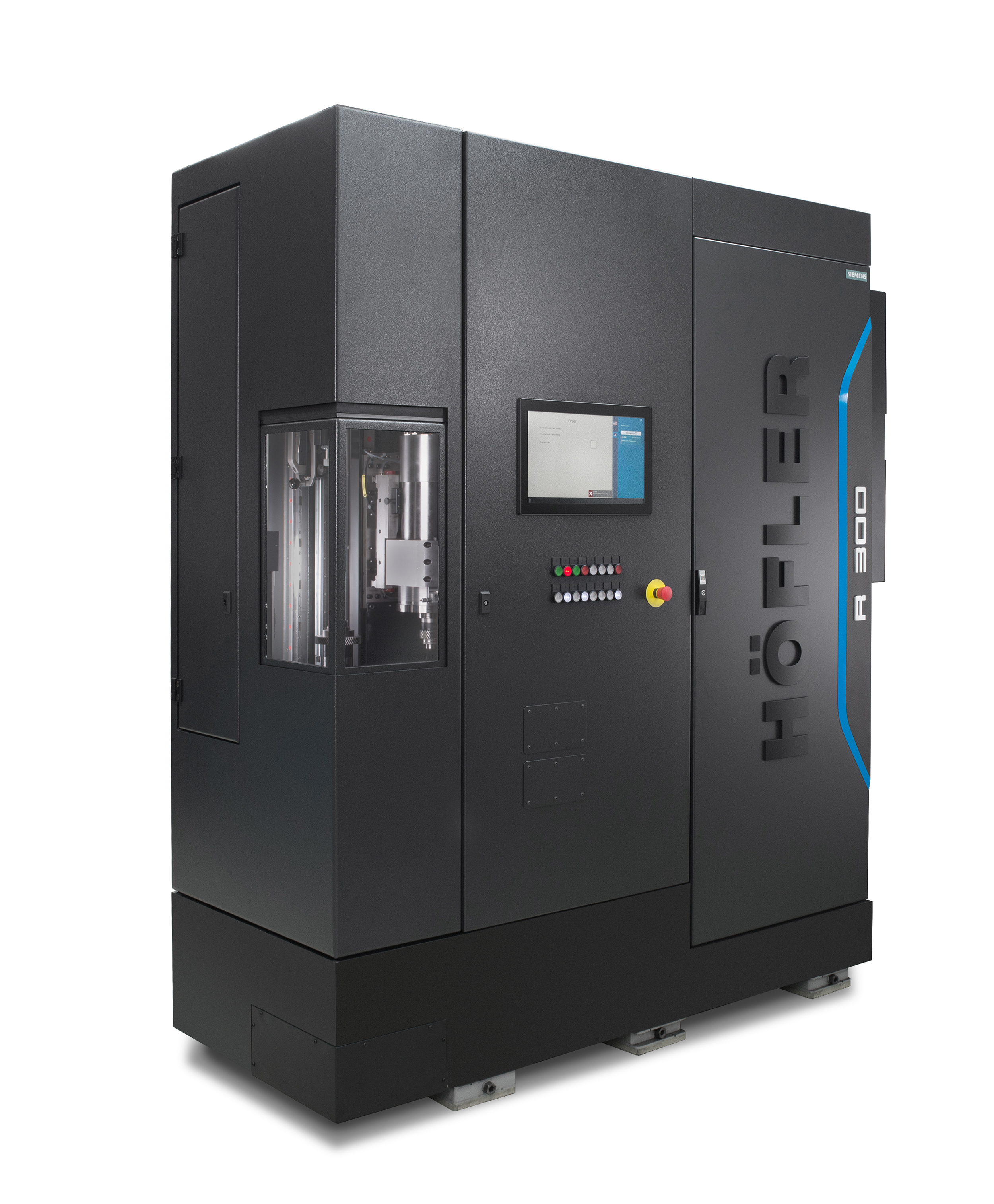
克林贝格的R300辊子测试解决方案可在生产周期内对齿轮进行100%的噪音评估。
“对于噪声分析,我们不仅通过查找振幅,还通过查找波纹度等规则结构,以更智能的方式评估形式误差。通过我们的GDA软件,我们为客户提供了一个工具来评估这种波纹度,并基本上接收可以直接与生产线末端测试进行比较的订单图。这确保了声学工程师与制造和质量工程师使用相同的语言,“Gorgels补充道。
今天重要的是先进的磨削过程模拟。如果发现齿轮有噪音,则出现的下一个问题是如何解决问题?与校正标准几何偏差相比,为噪声问题寻找技术解决方案要复杂得多。
“通过制造模拟,可以模拟不同的工艺偏差,例如翻滚磨削工具或工件台的扭转振动,可以模拟侧面波纹度的结果,从而与现实世界的测量结果进行比较。除了使噪音可见外,我们还帮助客户找到根本原因,“Gorgels说。
他今天看到客户印刷品上某些订单的公差更多。
“这些阶可以是齿网阶(和更高的谐波)以及所谓的幽灵阶。如果这些要求出现在打印输出上,则应在生产中进行测量。这增加了对标准生产解决方案的需求,我们提供GDA分析以及R300辊测试仪,“Gorgels说。
在未来几年,使用这些工具的需求将会增加。标准化将成为确保原始设备制造商与其供应商之间达成共识的主要话题。
利勃海尔指出齿轮检测结果的准确性、责任和可靠性
电动汽车中的齿轮对噪音产生有特别高的要求,因此对齿轮的表面结构和波纹度有更高的要求。虽然渐开线齿轮检测的测量原理仍然有效,但利勃海尔产品经理MatthiasBruederle表示,电动汽车齿轮今天正在推动齿轮检测的极限。
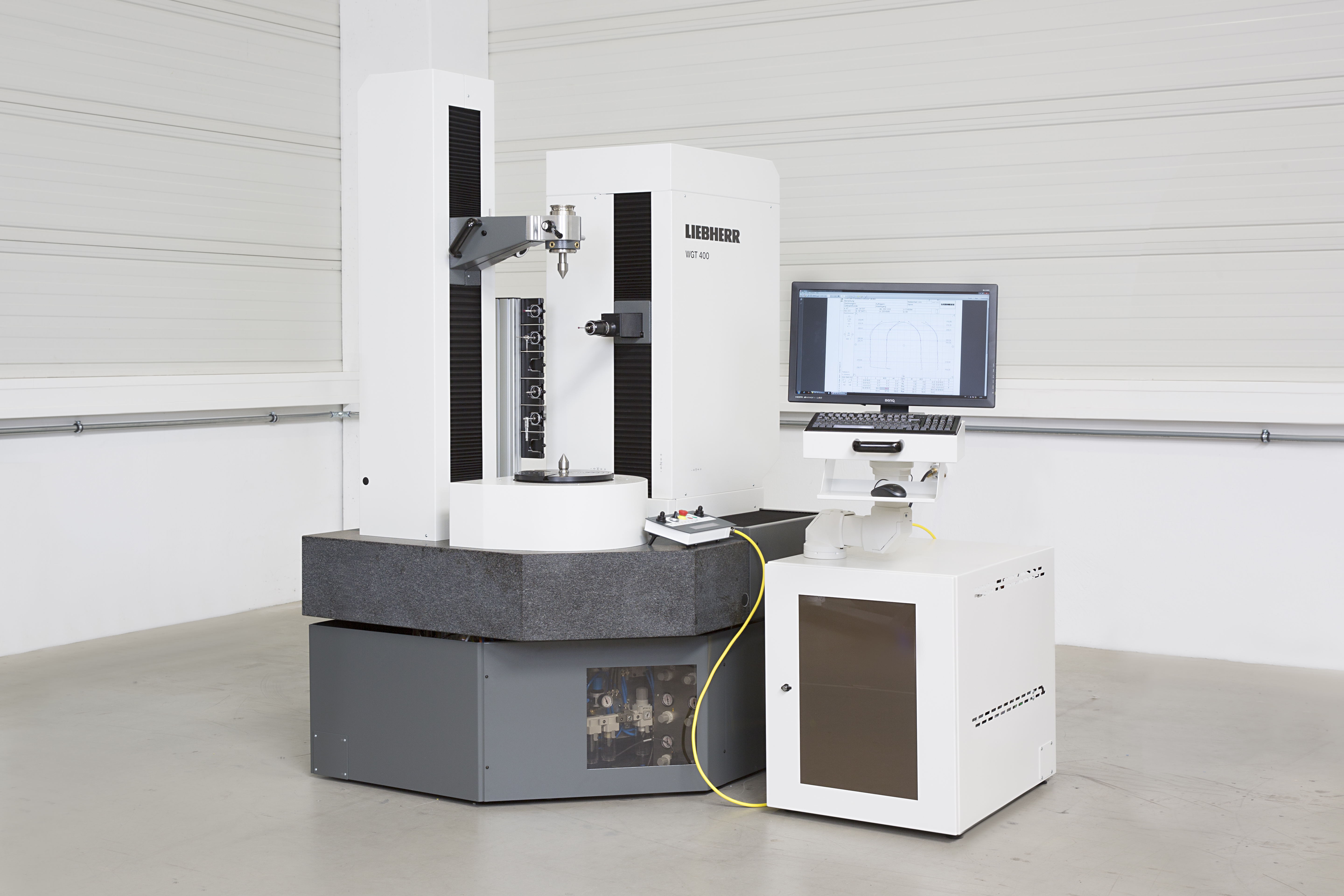
WGT400是一款通用齿轮检测机,适用于齿轮和刀具测量,是其他常见检测机的高质量替代品。
利勃海尔的WGT400优化了用于加工非常小零件的工具的测量精度和质量,包括内齿轮和具有非常小模块的齿轮。实时提供数据是机器的优势之一,也是其高测量速度。
WGT系列测量技术缩小了闭环领域的差距。四轴测量设备配备了高精度的机械和电子元件,由智能和用户友好的软件控制。花岗岩导轨和气垫的结合通过无磨损机械装置创造了最高的精度。
利勃海尔的解决方案“开放式连接”在磨床和检测中心之间提供了直接连接,提供了一种快速可靠的解决方案,以缩短对齿轮几何形状确定误差的响应时间。数据通过标准化的GDE接口传输,并与任何磨床配合使用。
“使用光学传感器似乎是提高性能和质量成本的适当解决方案,但是关于可达性和准确性的悬而未决的问题,特别是在抛光表面上,仍然阻止它成为适用于工业环境中检测的可靠解决方案,”Bruederle说。
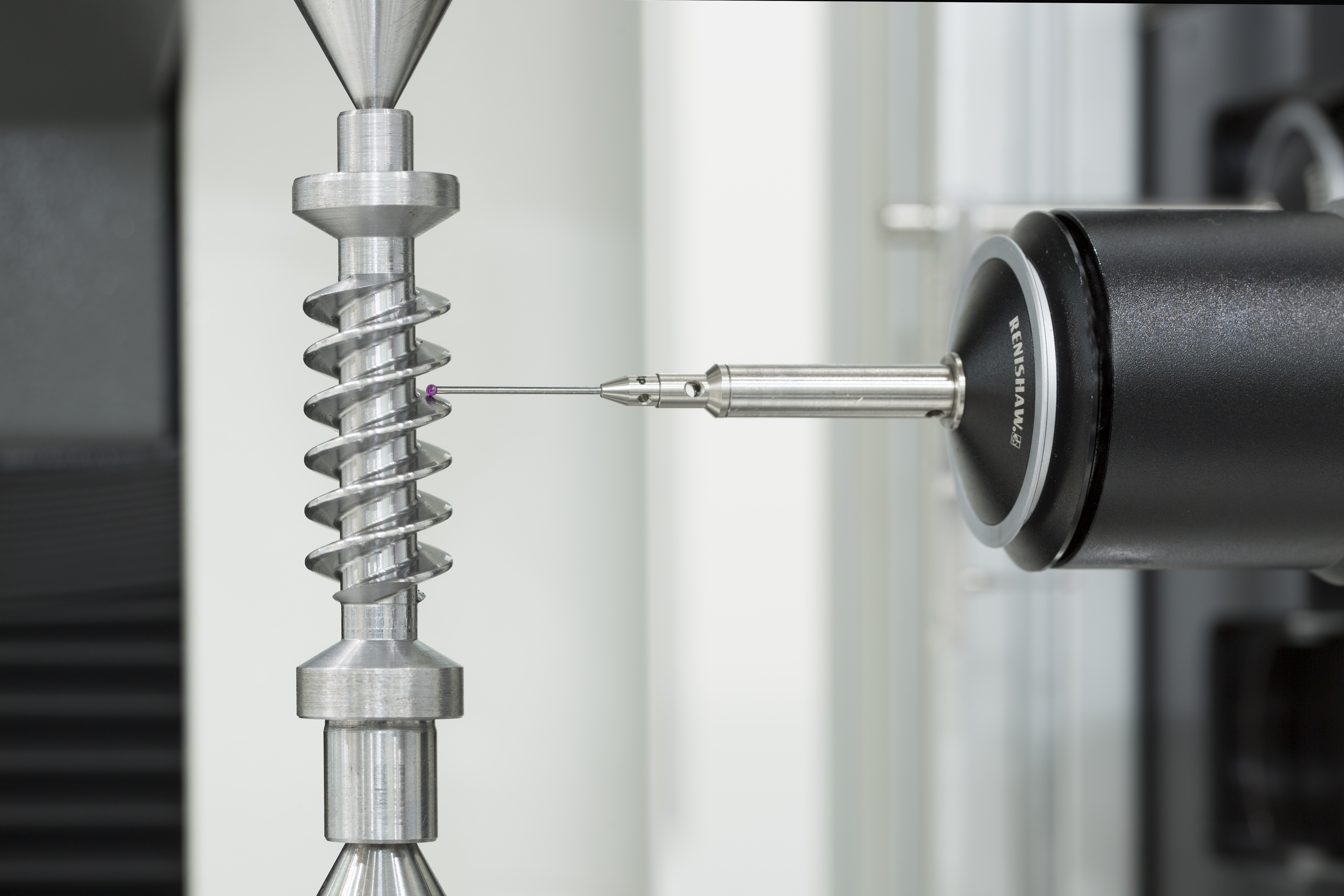
利勃海尔WGT280提供齿轮测量机,用于快速有效地分析最大直径为280mm的小齿轮
为了实现最有效的齿轮生产,Bruederle说,今天的检测结果必须提供最高的精度、责任和可靠性。“因此,测量速度和精度可能相互排除,并取决于齿轮几何形状。需要根据齿轮几何形状和生产方法制定特定的测量策略。
电动汽车扩展了齿轮测量解决方案,以满足汽车需求。
“开发新的生产方法,如齿轮齿的抛光和附加磨削工艺,目的是在齿面上随机分布磨痕,也称为静音移位磨削,在检测机上的硬件和软件组件的开发中找到了自己的方式,”他补充说。
用于评估表面粗糙度的传感器和软件扩展(需要特殊传感器)、评估专用端部浮雕以及评估和分析波纹度和起伏性将继续在电驱动齿轮的分析中发挥重要作用。
更高的检测水平
大规模的变速器制造需要更加关注动力总成中每个档位的噪声特性和质量。虽然电动机为未来的运输提供了多种优势,但它对隐藏齿轮噪音的作用很小。因此,新的检测设备和技术必须提供工具,为所有未来的电动汽车应用带来舒适性、可靠性和精确性。
(文章为小编翻译的作品,因翻译匆忙 如有不妥之处,请指正)